+ 40,000 products + 80 sectors
Tradition meets innovation
We have been synonymous with excellent craftsmanship and innovative felt solutions since 1861. Our high-quality wool and needle felts are manufactured in Germany and offer outstanding properties such as temperature resistance, sound insulation and durability. You can rely on our customised products, which are perfectly tailored to your individual needs.
Solutions made from design and acoustic felt
Some of our projects
For our future
Focus on sustainability
Innovative
Recycling technologies
Thanks to our innovative "LooPET" process, we can efficiently recycle and reuse post-industrial polyester waste. This flows directly into the production of new felt products.
Reduction
of the CO2 footprint
Our aim is to continuously reduce resource consumption and CO2 emissions. To achieve this, we are constantly optimising our production processes.
Made in Germany
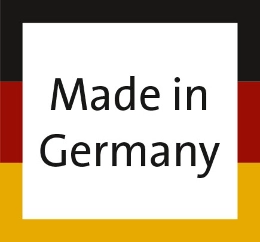
We produce exclusively in Germany and focus on the highest quality.
In our felt factory, we combine tradition with state-of-the-art technology to produce high-quality wool felts and needle felts for a wide range of applications.
Needle felt and wool felt are characterised by their durability and longevity, which saves resources. They also offer natural benefits such as temperature and moisture regulation and sound insulation.